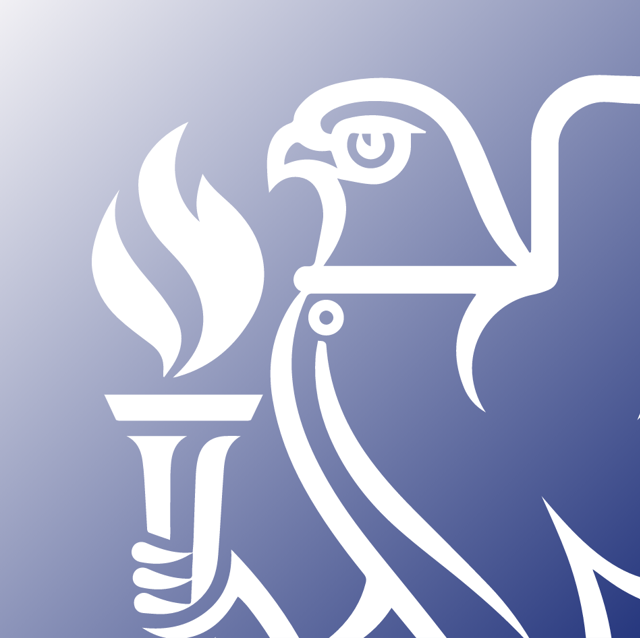
Article from the January 2015 edition of the CIBSE Journal written by Benjamin A Skelton.
Cyclone Energy Group's Benjamin Skelton explains what happened when the Walgreens drugstore chain set out to build the USA's first net-zero energy store - in one of the country's harshest climates.
The American pharmacy and grocery chain Walgreens is one of the biggest retail brands in the world, with more than 8,000 stores. So when, five years ago, it decided to build the first net-zero energy store in the US - in a way that would be as scalable as possible to the rest of its estate - the implications were enormous. There were other factors that made the project particularly challenging: Walgreens didn't want to change the operational nature of the building, so it had to have a conventional interior layout of about 1,350m2, and be open, if not all hours, then at least 50% more than a typical office. Because the company wanted to keep a close eye on the design and construction of the building, it was decided to site it in Evanston, near Chicago - close to its Illinois headquarters. With winter temperatures plunging to -240C, and summers as hot as 350C, it was hardly an auspicious location for a zero-energy building.
To be considered net-zero energy, the consumption of the store had to be 41% lower than the area average. The average annual energy consumption for a store in the Chicago area was 435,000kWh, so the building had to be designed to produce 256,000kWh in a typical year. Working with a solar photovoltaic company, Walgreens determined that the proposed building could produce this quantity of electricity using 840 micro-inverter panels on the roof, plus two 5kW vertical wind turbines. Given this fixed production capacity, the question was: how would the designers make sure the building's consumption was less than 256,000kWh?
Fabric and lighting
All aspects of the design had to be considered to get the building's energy consumption below the solar production estimate. The two largest uses of energy in a typical store are lighting and refrigeration, so the Walgreens team carefully analysed the efficiency opportunities in these areas. The fabric design, for example, increased the opportunities for daylighting - although this created further challenges. To maximise solar capacity, the store's typical rectangular design was changed to a tiered, multilevel, cantilevered roof with clerestory windows. This deviation from the standard brand design included significantly more glass. Moreover, a typical store has ribbon windows and a glass storefront, whereas this building incorporated an entirely curtain-walled west façade.
The west-facing fenestration meant that active and passive shading was needed. Glass below 4.3m was treated with automatic shade controls, regulated by an astronomical clock, limiting sun penetration to 1.5m. Direct sunlight was limited to a small distance to prevent cosmetic products from melting. For the glass above 4.3m, a light-redirecting film was installed. This sent 90% of the solar light and energy up and into the store, while 10% remained on path. This provided a thermal benefit and prevented glare at the sales counter. The film was applied to a third pane of glass and installed in the framing system of the curtain wall.
The wall and roof insulation were standard Walgreens specification, with U values of 0.28W/m2K and 0.19W/m2K respectively. When it came to artifi cial lighting, Walgreens installed its first all-LED system in 2010, and that is what this store received. The sales floor area has eight independent lighting zones with daylight-sensing controls. A typical store design includes 4kW of under-shelf LED lighting, to provide high levels of illumination on merchandise. This was identified as an opportunity for reducing energy consumption. Special fixtures chosen for the new store provide a unique light distribution pattern that produce s adequate luminescence levels, and allows under-shelf lighting to be removed.
HVAC and refrigeration
A standard Walgreens store uses constant volume rooftop units for heating, ventilating and air conditioning (HVAC). As the roof was covered with solar photovoltaic panels, all the equipment had to be internal. A lso, as the store came right to the edge of the site boundary, there was only a very small balcony for air-cooled heat-rejection equipment. With LED lights and daylight controls providing a minimised load, the largest remaining opportunity for energy savings was the refrigeration system. The design team searched for a system that could capture the heat rejection from the refrigeration system and create useful heat.
Chicago is a heating-dominated climate - with 6,536 heating degree days - and heating is the largest annual HVAC energy end use. Walgreens had completed a geoexchange store in Chicago previously, and this was considered the best means for capturing the waste heat from refrigeration and using it for HVAC. Eight, 152m vertical geo-exchange wells were designed below the parking lot, and the design team considered several HVAC options, including distributed heat pumps and heat pump rooftop units. Ultimately, a chiller-heater central heat pump system was selected for this store, based on the wholebuilding energy analysis. In addition to net-zero operation, Walgreens had set a secondary goal to create a store that us es only natural refrigerants. With a central heater-chiller heat pump, options existed for a system with a carbon dioxide (CO2) refrigerant. No manufacturers were available in the US, but a couple of options were found in Europe.
However, the decision to use this system was made only 10 months before the store was due to open. Aware that getting a custombuilt heat pump from Europe posed a risk to the opening schedule, the design team had a US-produced substitute, R-134a-based central heat pump on standby. One requirement of using a CO2 refrigerant heat pump was that the system had to meet Underwriters Laboratories (UL) testing requirements to be permitted for use in the US. UL certification is a common mandatory requirement of insurance companies and code jurisdictions, and requires that refrigerant piping and systems be tested and certified at five times the rated operating pressure. Given the high operating pressure of CO2 (80 to 100 bar), this requirement seemed excessive, but the system passed the tests. It was shipped to the US and made it through customs with no issues.
The transcritical CO2 heat pump has three sets of variable speed compressors: low temperature, servicing the evaporators for the freezer ; medium temperature, servicing the evaporators for the cooler ; and high temperature, servicing the chilled water system . The heat rejection for the heat pump is used for hot water and service water. The geo-change serves as a battery, storing heat rejection from the cooler/freezer evaporators for use as heat when needed. With the central systems determined, and a solution found to capture waste heat from the refrigeration system, attention turned to the comfort systems. With low-temperature chilled water and water heating readily available, a four-pipe fan-coil system was designed. Initially, a radiant heat design was included, but this was removed to help meet budget constraints.
The sales fl oor area was split into three thermal zones with variable-speed, singlezone, air handling units hanging in the space. Ductwork was designed architecturally as a straight length off the air handling units, with diffusers discharging directly down into the space. The ductwork transferred air to the space effectively, but what wasn't anticipated was the noise level. At fan speeds above 80%, the air handlers created signifi cant fan noise - more than was acceptable for Walgreens operations. So they were limited to 80% maximum speed, which did not have an impact on cooling, but severely hampered the ability to provide heating. A dedicated variable air volume, outside air handling unit was provided to decouple the ventilation load. The unit regulates outside air volume based on demand. The store has a highly variable occupant load and, by using CO2 sensors throughout the sales area, ventilation load is minimised.
Measured performance
Walgreens recognised the opportunity to use this store as a research project. A central building automation system was installed, with remote monitoring and control capabilities. Additionally, a branch breaker, electrical sub-metering system was installed, to measure real-time loads from nearly every piece of equipment in the building. With a detailed measurement and control system, the team was able to monitor hundreds of data points, and fi nd areas where the operation was deviating from the design. After almost a year, the results show that - in the first 12 months - the store will fall short of net-zero energy consumption. There are several reasons for this. Chicago experienced one of the severest winters in record ed history. The design energy model was created using average weather files (typical meteorological year) and included a buffer to account for weather swings. However, with a mean temperature of -8.1° C in January 2014, the extreme cold exhausted most of the buffer.
As-built documents detailed that the curtain-wall system underperformed against the design requirements. The installed system exceeded specifi ed fenestration cent re-ofglass performance; however, the framing system was not thermally broken, causing the assembly to under perform at peak conditions by 12%, further exhausting the net-zero buffer. The automated shades served as valuable insulation, and were used at night to help maintain space temperatures. With a heat pump design never before attempted on this type of building, it was expected that there would be performance issues. The gas cooler - which was provided to help remove excess heat and prevent the geo-exchange fi eld from becoming overheated in the cooling season - had problems with electrical overloading and was off for most of the first summer. Also, it was determined that the compressors initially provided were oversized. The gas-cooler issue was resolved and the compressors replaced, and energy reductions are being observed.
Humans cause energy waste. This store is not used by high-tech engineers and, while the system is designed to operate automatically, the employees and customers have an impact on its energy consumption. A revolving door was engineered into the project, replacing an air lock, but it did not have good thermal properties, and was not well sealed. A disabled access door was still required, but this did not have an air lock. Rather, an air curtain was installed to minimise air infiltration when in operation. It was found that a high percentage of nondisabled customers used this door, and the air curtain proved ineffective. Given all of these issues, the path to netzero status is clear. Using the measurement and verification system, and a calibrated energy model, the store is being fi ne-tuned to reduce energy consumption by 5,000kWh per month.
Lessons are still being learned on this project, but the net-zero approach has been recognised with LEED Platinum status, Green Globes certifi cation, and a Green Chill Platinum rating from the US Environmental Protection Agency. Walgreens' net-zero Chicago store could pave the way for radical changes in the US retail landscape.
Technical Symposium award winner Benjamin Skelton's paper 'It's not easy being green' on the design of the Walgreens store was named the "Most significant contribution to art and science of building services engineering" at the 2014 Technical Symposium.
Booking open for 2015 Technical Symposium
The 5th CIBSE Technical Symposium will be held on 16 and 17 April 2015 at University College London. The event encourages participation from both young and experienced industry practitioners, researchers and building users to share experiences and develop networks. The 2015 Technical Symposium will address the theme: Simple buildings, better buildings? Delivering performance through engineered solutions. To book your place visit www.cibse.org/symposium
Ten key lessons
Here are the top lessons learned on the project: Don't rush. The design team had less than one year to do something never done before and that is not enough time to evaluate opportunities. When innovating, don't forget the fundamentals. Keeping systems as simple as possible will net best results. Require total system thermal performance data on fabric systems. Getting a worseperforming curtain-wall system permanently impacts the performance of the store. Engage all contractors early. While contractors knew the net-zero ambition, they were engaged too late in the process to feel any sense of ownership of the greater goal of the project. Many set-up and configuration issues could have been avoided.
Commission all building systems as early as possible. Once a building goes into operation and is considered substantially complete, getting contractor support is very difficult.
Energy meters don't always tell the correct story. If not for calibrating the design energy model to the store operation, it may never have been noticed that our measurement and verification system was configured incorrectly. Air locks perform better than revolving doors. Customers will go for the easy option, and revolvers require more work than hitting an automatic door-opener button. Geo-exchange couples well with transcritical CO2 refrigerant heat pumps as it provides a steady condensing temperature (<15° C). Technology cannot overcome humans. No matter how well you design an automation system, people can make a mess of it. Don't start your net-zero performance period in a historically severe weather season!
Walgreens' Project Team
- Client: Walgreens
- MEP: WMA Consulting Engineers
- Architect: Engineer + Theodore
- Energy consultant: Energy Center of Wisconsin
- Commissioning/ energy consultant: Cyclone Energy Group