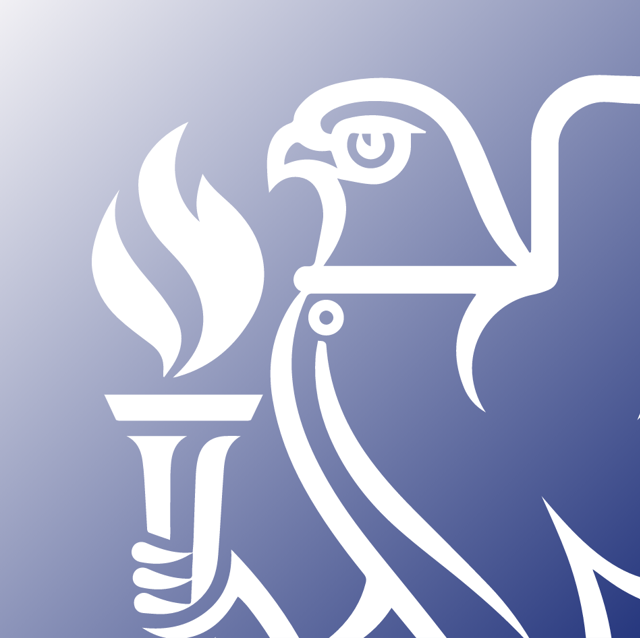
Back to CIBSE Case Studies Overview
Article from the September 2013 edition of the CIBSE Journal written by Andy Pearson.
The Mary Rose Museum opened earlier this year, but the painstaking process of drying the warship's ancient timbers goes on. So how did Ramboll achieve a closely controlled environment in one of the UK's busiest tourist attractions?
It is not often that a museum of medieval history is completed before its star attraction. But that was the case with the new Mary Rose Museum in Portsmouth Historic Dockyard. Designed by Wilkinson Eyre and interior architect Pringle Brandon Perkins + Will, the £27m visitor centre opened to critical acclaim earlier this year.
The problem was that the museum next to HMS Victory had to be built around its incredibly delicate centrepiece, a 20m x 13m section of the Tudor warship's starboard hull. This is currently saturated with timber preservative as part of a conservation process that will not be completed until 2016.
"The hull's precarious condition meant that conservation had to continue, without interruption, while the Mary Rose's new home was built around it," says Tim Lloyd, an associate at building services engineer Ramboll UK. Not only did the services have to be designed to maintain the environment around the hull during construction and the museum's first years as a busy tourist attraction, they also have to be capable of being entirely reconfi gured in 2016, when the building will be converted into a more conventional visitor centre.
Up she rises
To appreciate the challenges that had to be tackled in developing the engineering design for this unique museum, it helps to understand how the hull was salvaged. Having been embalmed in her watery Solent grave for centuries, the Mary Rose's 1982 recovery operation was, and still is, the largest underwater maritime archaeological excavation ever attempted. In addition to the 280-tonne section of hull, the excavation also produced an astonishing collection of 19,000 16thcentury treasures.
After it was retrieved from the seabed, the wooden carcass was placed in No 3 dock at Portsmouth Historic Dockyard, where the painstaking task of conserving its ancient timbers commenced. A tensile fabric enclosure, known as the Wemyss building, was erected over the dock. Suspended inside this was an insulated enclosure of foil-facedinsulation, termed the "hot box" by the engineers, which was designed to keep the environment around the hull at a constant 25-27 degree C. Heating was provided by radiant panels placed beneath the steel cage that supported the hull and hot box, while cool air was drawn from within the confines of the dry dock. Inside the insulated box, the timbers were initially sprayed with a fine mist of chilled water to stabilise them, and later with an aqueous solution of polyethylene glycol (PEG) wood preservative solution.
The new museum was built around the tented building to enable the PEG spraying to continue, uninterrupted, 24 hours a day, seven days a week. The woodclad building's low, elliptical form was dictated partly by the parabolic geometry of its roof and partly by the need to minimise the space around the hull to make it easier to maintain the strict environmental conditions necessary for its preservation.
The designers set out to evoke the dark claustrophobic atmosphere on board the medieval ship. The salvaged hull, still cocooned within the hot box, is located on one side of the museum. Facing it, a virtual port side has been created, containing three decks of galleries housing the original artefacts in a mirror image of where they would have been found on the starboard side. Walkways divide the hull from its recreated twin, while galleries at the prow and stern of the museum provide a theatre and further displays on the ship's crew, the cook, the carpenter, the surgeon, containing personal possessions and professional tools.
Heat from the artificial lighting is minimal because the galleries are dimly lit; what light there is has been focused on the cabinets housing the salvaged artefacts of everyday Tudor life. These require tight environmental control and are housed in highly controlled display cases (see box opposite). And through windows in the hot box, visitors can glimpse the 500-year-old hull itself.
Gently does it
PEG spraying finished earlier this year and the hull is currently wrapped in a series of textile ducts while its timbers are being dried. Conservationists estimate that between 110 and 130 tonnes of water were trapped in the timbers following the years of PEG spraying. The task was to start drying the timbers as quickly as possible to prevent mould growth. It is expected that most moisture will be drawn out during the first year, but it will take up to four years before
the wood is fully dry.
Unless the environment around the ship is controlled to ensure the timbers dry evenly, they could crack and deteriorate.
With the hot box now contained within the museum, its heat losses are small. "If you designed a ventilation system to meet the actual heating load, the volume of air needed would only be around 1-2m3/s", says Lloyd. However, this quantity of air would be insufficient to maintain the close control conditions needed inside the 40m long, 16m wide, 13m high space. Ramboll's solution has been to significantly increase the volume of the air supply to the box, but to target it onto the hull. Conditions required for successful drying are 19 degrees C +/-1 degrees C, with 54% relative humidity +/-4%. To design the air distribution, the remnants of the ship and its enclosure were laser-scanned to create a precise model. Engineers then used this to test various ventilation and cooling techniques, and to check air velocities, dwell times and shear stresses created by the air movement to find the most effective. "Using computational fluid dynamics (CFD), we found that the minimum volume of supply air we could use that would maintain the correct conditions around the ship was 25m3/s," Lloyd explains.
The precise location of the ducts and position and number of holes in the ducts were also arrived at using CFD analysis. The designers were aiming to cloak the ship in conditioned air that had a maximum velocity of 0.25m/s adjacent to the hull. "The boundary conditions are absolutely critical if the hull is to dry evenly," says Lloyd.
Ordinary textile ductwork, which allows the air to permeate the walls of the duct, would not provide sufficient control of the supply air. Instead, impermeable ductwork was used, with laser cut holes to control and direct the air supply.
The textile ducts are attached to a stainless steel and titanium suspension system, which was installed while the hull was still being sprayed. The ducts were then attached to the suspension system during the switchover phase and plugged into preinstalled ventilation plant. "It was important that, as far as practicable, everything was ready for the changeover from spraying to drying to ensure it happened in the shortest possible time."
Three air-handling units (AHUs), hidden in the dry dock, supply 8.3m3/s of air each. The air is distributed via two 1,200mm diameter ducts that run the length of the hull; these drop down to supply 14 smaller ducts that weave in and out of the timbers like giant worms. The air system is fully recirculating, with extract air dried and returned to the hot box at boundary
conditions.
Lloyd describes these AHUs as "a bit of a work of art". To build in robustness, the AHUs make use of fan wall technology, so instead of a single fan there is a wall containing six inverter speed-controlled fans. Each unit will operate at 80% peak demand so that, if one fan fails, the speed of the other five can be ramped up to make good the loss. In addition, each heating and cooling coil is split into three sections, with two of the sections capable of supplying the duty required. The three AHUs feed a common air supply header.
Heating and cooling plant is located in a plant room at the north of the building. There is no gas supply so the two heating boilers are oil-fired. There is, however, a dock steam main so the plant room includes a heat exchanger, which is the primary source of heat for the building in winter.
Cooling is from three packaged aircooled chillers, which circulate water around a primary loop. Two secondary circuits connect to this, one to feed the hull AHUs and the other to feed all other services within the building. To maximise the AHUs' ability to dehumidify the air, the chilled water is supplied at 2 degrees C (with a 6 degrees C rise); for the chilled water circuit serving the main part of the building, the chilled water is mixed to bring it up to a 6 degrees C supply temperature. However, to save energy the chillers operate at the raised temperature of 6 degrees C when dehumidification loads are minimal.
A small AHU located in the first-floor plant room supplies fresh air for the visitors and pressurises the space. To ensure no more outside air is supplied to the system than is necessary, the AHU has a variable speed fan, with the extract rate balanced to maintain the museum at a positive pressure.
"Sensors in the extract duct will monitor humidity levels so that on a rainy day, when visitors enter with wet clothes, we can ramp up both supply and extract rates to capture the moisture at source," explains Lloyd. In addition to the fresh air supply, the galleries are fitted with two fan-coil units on each floor to provide additional cooling for peak loads.
All the ductwork and headers for the system are already in place to allow a swift changeover between the drying and final display modes.
Ready for its public
In 2016, when the timbers are dry, the hot box will be dismantled and the fabric ducts removed, allowing visitors to gaze directly at the hull from the galleries. "From an environmental perspective, that means there could be 150 people present at any one time in what is, effectively, a giant display case containing the hull," Lloyd explains.
The system has been designed to enable the changeover to be completed swiftly and with minimum disturbance. "All the design work has been done so that at the flick of a switch, and by moving a few dampers, the environmental systems will be transformed from hull-drying to hull-display mode," says Lloyd.
To develop the final display solution, the engineers returned to the digital model of the ship to examine conditions around the hull with the hot box removed. Correct air movement is critical, even when the hull has dried, to maintain stability of the timber. The CFD analysis showed that the best way to avoid areas of stagnant air was to supply conditioned air at a number of levels using directional air-jets.
As part of the changeover, the visitor walkways used by the visitors will be fitted with air locks between the galleries and the ship hall. The same three AHUs currently used to dry the hull will be reused to maintain the environment within the ship hall. The units will be configured to run in recirculation mode with two operating and one on standby.
When the works are completed, the Mary Rose hull will be on display a short distance from the mudflats where Tudor craftsmen first assembled the vessel hundreds of years ago. The museum will be a fitting tribute to their work, to the years of careful restoration and to a cleverly designed ventilation system that will enable the hull to be preserved for generations to come. CJ
A case-by-case basis
Many of the display cases manufactured by Reier feature a micro-air conditioning system to help preserve the delicate leather and wooden artefacts on display. Conventional museum cases usually control only the humidity of the cabinet; they do not have temperature control but instead rely on the temperature of the room in which they are housed to be kept constant. However, the small size of the galleries and the large numbers of expected visitors meant that this was not possible at the museum. Instead units are fitted with a thermoelectric Peltier heat pump unit, to filter and humidify the air and provide heating, cooling and dehumidification. Each cabinet has its own electrical supply and chilled water connections.
The Project Team
Client: The Mary Rose Trust
Architect: Wilkinson Eyre Architects
Interior architect: Pringle Brandon Perkins+Will
Consulting engineer: Ramboll UK
Cost consultant/CDM Coordinator: Davis Langdon (Aecom)
Exhibition design: Land Design
Main contractor: Warings