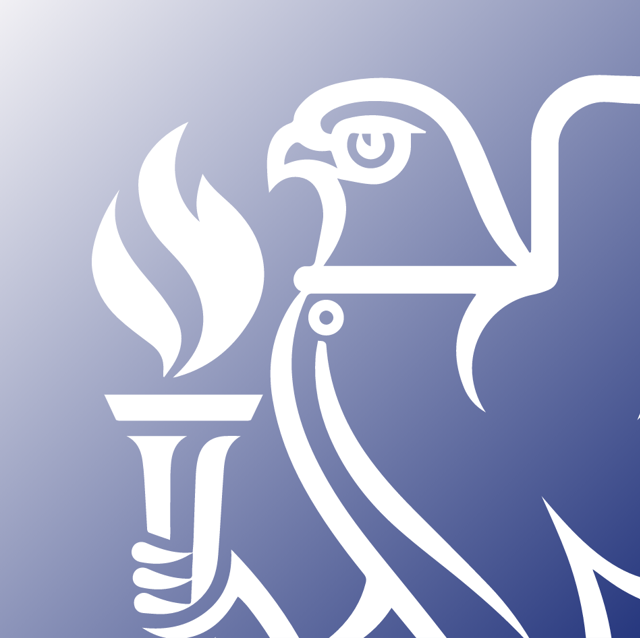
Article from the June 2014 edition of the CIBSE Journal written by Andy Pearson.
Visitors doing their weekly shop in Tesco's new Wisbech store will be blissfully unaware that they are shopping in one of the most advanced and energy efficient supermarkets in the UK.
The 5,600m2 building cost no more than a standard Tesco, yet it incorporates a host of new technologies, including the UK's first store-based CO2 refrigeration heatreclaim system. "We set out to push the technology, to achieve as much as we could within the confines of a standard store build cost," says Rob Redfern CEng MCIBSE, engineering project manager at Tesco's UK property development and engineering arm.
Four weeks after opening, the Cambridgeshire shop is on target to emit 15% less carbon than a standard store.
Tesco's Wisbech branch is another small step towards the company's aim of halving emissions per square foot from its stores and distribution centres by 2020, compared to a 2006 baseline. By 2050, the retail giant is aiming to be a zero-carbon business. "Our focus on being more energy efficient will serve to further progress our carbon targets and to reduce our exposure to rising energy costs," says Redfern.
Electricity consumption is the largest source of carbon emitted from a standard Tesco store. Refrigeration accounts for about 40% of total electricity usage, and lighting for another 25%; the actual proportions vary slightly from store to store, depending on the shop's design, and the efficiency and effectiveness of the technologies installed.
According to Redfern, Tesco is "always striving to find new technologies with a smaller carbon impact than our existing equipment". Before any technologies can be installed in a store, however, they have to pass Tesco's engineering and maintenance trials. This assessment is based on customer experience, and on an evaluation of how they impact on the look and shopping experience for customers.
Trial lengths vary depending on the technology; however, because building services technologies often have to operate under changing seasonal conditions, this can mean a minimum of a year's operation before approval is granted. "Our governance process, which considers maintenance, energy, carbon, capital cost and impact on customers and colleagues, ensures that any proposed new equipment has a robust business case for it," Redfern explains.
In terms of construction and layout, the Wisbech store is not significantly different from any other Tesco Extra. It was selected as the venue for the retailer's latest batch of technology trials because the lead time was long enough for the engineering team to establish which technologies should be trialled, and to obtain the necessary approvals. "This store gave me the opportunity to affect its design at an early stage," says Redfern.
"From around 100 initial suggestions for possible technologies, we whittled the list down to 15 that we felt were achievable and would give a good return on investment."
The Wisbech store opened its doors in February, and is part of a larger retail development, which includes a cinema, restaurants and a gym. The single-storey building is raised above the ground on a steel-framed podium, which accommodates a shared car park beneath. The supermarket is supported on a steel structural frame, which supports both the roof and a rooftop plant well, tucked out of sight at the rear of the store. The plant well is home to four air handling units (AHUs) and two refrigeration packs. These packs include compressors, heat exchangers, controls and the electrical panel, and are connected to the condensers. The majority of the heating, cooling and refrigeration services distribution takes place at high level above the sales floor.
From a carbon-saving perspective, the most significant technological change at Wisbech is the addition of a heat-reclaim system on the CO2 refrigeration circuit. All of Tesco's new Superstores, Extra stores and Metro stores use CO2 as a refrigerant for the freezers and chilled food cabinets. However, Wisbech is the first UK supermarket to take advantage of the relatively high temperature of the CO2 system by capturing this heat. As a result, in winter, instead of dumping the waste heat to atmosphere, a heat-reclaim system will extract the heat using a series of heat exchangers for use in the store.
CO2 heat exchanger technology has not been trialled in a retail store until now because of the challenge of dealing with the high system pressures required in CO2. However, Redfern says Tesco has learned from the experience of dealing with CO2 since it was first introduced in 2009. This, he says, has given Tesco the confidence to trial the heat-reclaim system at Wisbech.
"I would like to think that the use of natural refrigerants by the retail industry, and the increased demand for them, will help to make natural refrigerant-based systems more competitive, and available for all future applications, not just retail," says Redfern.
Tesco's calculations show that the refrigeration heat-reclaim system has the potential to deliver a peak duty of 400kW heat when running transcritical, which, according to Redfern, is when the refrigeration cycle passes through the critical point (see CPD, CIBSE Journal, December 2012). At the same time, the retailer's calculations show that the peak heat demand for the store is 600kW in winter. To make up the 200kW shortfall when the system is running transcritical, Redfern says it will be possible to boost pressure in the CO2 system to enable more heat to be extracted. However, this option will increase the system's electricity consumption. For this trial, the additional 200kW will be supplied by five wall-hung, gas-fired condensing boilers.
With the store in operation, Tesco will monitor the system to establish whether, and at what point, it is beneficial to increase electricity use to enable the system to provide additional heat, or whether it is more cost effective to use the boilers. "In the first four weeks since the store opened, the boilers have not run, other than for testing, no gas has been used, and the refrigeration system has not needed to be run transcritical," Redfern says.
The CO2 heat exchangers transfer the captured heat to the low temperature hot water (LTHW) system, which supplies both the AHU heater batteries and a higher temperature circuit servicing the hot-water system calorifier and radiant panels. A ducted air system supplies the reclaimed heat to the retail floor.
The Wisbech store also incorporates a radiant heating system to provide additional heat to the checkout areas and customer service desk. The technology was introduced in response to comments, from customers and staff at other stores, about the need for more heat in areas where people are likely to be stationary. "Every comment from customers and colleagues helps us to make improvements," says Redfern. "The changes at this store are in response to comments, made in 2012/13, that informed us we needed to make our stores warmer." He says feedback on the new addition at Wisbech has been "very positive".
In summer, the store uses Tesco's standard "free cooling" solution to cool the retail floor. This is based on chilled air, drawn from the chilled food aisles at about 10-14 degrees C which is then supplied as cooled air to the warmer ambient areas of the shop floor, a process Redfern refers to as "cold air retrieval". "We don't usually need additional cooling coils because there is enough cooling capacity in the retrieved cold air," he says. The system is being trialled in reverse mode, too, at Wisbech, so that heat from the heat-recovery system can be used to warm the air supplied to the cold aisles if required.
Improved internal environmental conditions have also been achieved with the installation of a new main-entrance door air curtain. "There is a misconception that our design-standard, over-door air curtain should provide heating for the store," says Redfern.
At Wisbech, a new model of air curtain without heating is being trialled. It is hoped it will provide an improved curtain of air over the entrance-door opening, to help maintain the positive air pressure within the store, but without adding to the heat load on the heatrecovery system.
Alongside its innovative heat-recovery system, lighting is the other main area in which the Wisbech store differs from the Tesco norm.
Externally, the store and undercroft car park are lit using low-energy LED technology, and LEDs are a significant feature internally, too. At Wisbech, they are used for all store accent lighting, with the exception of the clothing area which, at the time, was not ready to switch to LED technology. In addition to it being more energy efficient, by using elongation lenses on the LEDs that illuminate signage, Tesco has also been able to focus the light accurately where it is needed, which, in turn, has reduced the number of accent lights required.
"The biggest challenge with the change to LED is the increased capital cost of the lamps," says Redfern. Nevertheless, despite their increased cost, LEDs will be used by Tesco to light the interior of all its new Superstore and Extra supermarkets this year. The additional capital cost will come from Tesco's annual energy-reduction budget.
To further reduce lighting loads at the Wisbech store, rows of roof lights allow daylight to reach the sales floor. A DALI lighting control system, which is standard in all of Tesco's larger store formats, controls illuminance levels, day and night, to maximise energy efficiency. The lighting panel will also self-test the emergency lighting system.
While lighting for back-of-house areas is controlled using movement sensors; salesfloor lights are dimmed based on daylight control, with additional time-clock control to take account of the varying trading times.
All key energy-consuming assets are measured and monitored at Wisbech using Tesco's remote system house, based in India. Here, a team keeps a constant watch on the energy consumption of all the UK stores. "We are able to monitor voltage, current, power, kWh in half-hourly data, and more," says Redfern. This will enable Tesco to monitor the Wisbech store's history of energy use, keep track of energy consumption, spot exceptional or excessive use of energy, and, if necessary, mobilise Tesco's 1,000-strong UK maintenance team to fi x any problems.
A further eight team members at the system house analyse energy consumption in stores. They identify hotspots and long-term trends to help Tesco focus its energy -saving efforts. "We have a team of data analysts who will compare the performance of the Wisbech store with others in the estate to benchmark its performance," says Redfern.
A typical Tesco Extra store emits about 2,000 tonnes of CO2e a year. " We have calculated the savings to be in excess of 350 tonnes of CO2e, based on electricity and gas use," Redfern explains.
More impressive, given the savings in CO2, is that the capital cost of the new technologies is 3% less than for a standard store. According to Redfern, the over-door air curtain resulted in the biggest capital cost saving "due to the reduction in pipework needed". However, he anticipates the largest energy saving will come from the heat -reclaim system.
Redfern says monitoring the new technologies will help the supermarket in discussions with Building Control. At the moment, heat rec laim from the chilled -food refrigeration system, and free cooling using cooled air from the chilled aisles, are considered process loads by Building Control; as such, they are not fully recognised in the Part L compliance calculations. "It is an issue that needs to be addressed," he says. He might have a point because, at Wisbech, such technologies are contribut ing to a 15% reduction in carbon emissions. CJ
How the heat reclaim refrigeration system works
The system was introduced at Wisbech to demonstrate the viability of using waste heat from the CO2-charged refrigeration plant as the base heat source for domestic hot-water systems (DHWS) and the air handling unit (AHU) heater batteries.
The DHWS and radiant heat load is 100 kW. The store heating requirement is 500 kW. The store has two dual-temperature refrigeration packs, each fitted with two heat exchangers: a 65 kW heat exchanger for the 80 degrees C DHWS and radiant heating header, and a 140 kW heat exchanger for the AHU's 50 degrees C header. The heat exchangers are treated as the primary boilers for water circulation.
The DHWS is supported by two condensing, gas-fired boilers. The AHU system is supported by three condensing gas-fired boilers sized for 66% of the total load. Each heat exchanger CO2 circuit is fitted with a three-port bypass valve in the return flow. The gas cooler, sized at 110% and fitted with fan speed control, has a three-port bypass in the return. This configuration provides seven possible configurations of gas cooling:
- Gas cooling alone
- DHWS
- DHWS + gas cooling
- AHU
- AHU + gas cooling
- DHWS + AHU
- DHWS + AHU + gas cooling.
The combined heat rejection is sufficient for some periods of the year, but during peak heat loads, or periods of low refrigeration duty, the plant must run transcritical to meet the heat requirement. This condition can be forced using the modulating valve in the return from the gas cooler, which can raise the head pressures from the normal 50 bar to a maximum of 80 bar.
Construction Team
Consultants - URS
Main contractor - Bowmer & Kirkland Ltd
HVAC contractor - Neville Tucker
Electrical contractor - Halsall Electrical
Refrigeration contractor - Space Engineering